Stainless Steel Seamless Casing Pipe
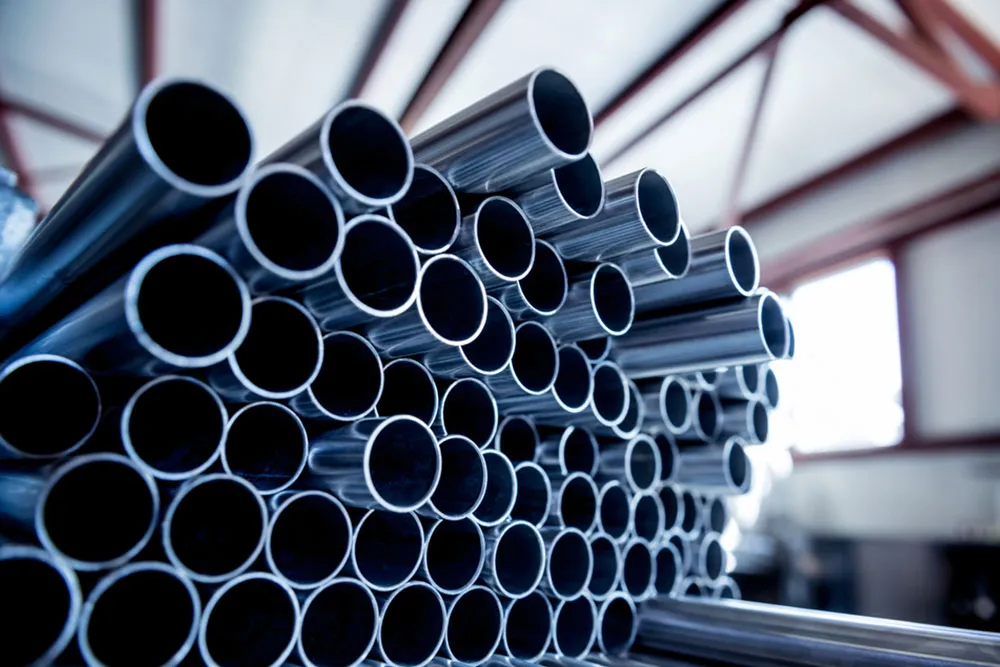
Outline: Stainless Steel Seamless Casing Pipe
Section | Subtopics |
---|---|
Introduction | Overview of stainless steel seamless casing pipes |
What is Stainless Steel Seamless Casing Pipe? | Definition, Manufacturing Process, and Key Features |
Key Materials for Stainless Steel Seamless Casing Pipes | TP304H, TP310H, TP316H, TP321H, TP347H: Characteristics, Benefits, and Applications |
Understanding Pipe Sizes | Diameter Options (OD 4 1/2” to 20”), Thickness (5.12mm to 16.13mm), Lengths (R1, R2, R3) |
Manufacturing Standards | ASTM A213, ASTM A376, ASTM A511, ASTM A312, DIN 17459, EN10216-5, GOST 9941-81 |
Certificates and Approvals | LR, BV, DNV, GL, ABS, KR, CCS, TS, PED, AD2000, ASME II, III |
Applications of Stainless Steel Seamless Casing Pipes | Oil & Gas, Power Generation, Water Treatment, Chemical Industries, and more |
Benefits of Stainless Steel Seamless Casing Pipes | Corrosion Resistance, High Strength, Durability, and more |
Types of Stainless Steel Seamless Pipes | Grades and Differences between TP304H, TP310H, TP316H, TP321H, TP347H |
Surface Finishing of Casing Pipes | Types of Surface Finishes and Their Impact on Performance |
Welding and Fabrication of Stainless Steel Casing Pipes | Techniques and Considerations in Welding |
Quality Control in Manufacturing | Testing Methods, Inspections, and Standards Compliance |
Packaging and Delivery | Export Standards, Packaging Options (Wooden Boxes, Bundled), and Transportation Considerations |
Comparing Stainless Steel Seamless Casing Pipes with Other Types of Pipes | Differences between Seamless and Welded Pipes, Benefits of Seamless Pipes |
Maintenance and Care for Stainless Steel Casing Pipes | How to Extend the Life of Stainless Steel Pipes |
Conclusion | Recap and Final Thoughts |
What is Stainless Steel Seamless Casing Pipe?
Stainless steel seamless casing pipes are made from high-quality stainless steel and are manufactured without any welds or seams. This ensures the pipe is stronger, more durable, and resistant to leakage. The manufacturing process for seamless pipes typically involves extrusion or rotary piercing, which creates a pipe with uniform thickness and a consistent internal structure.
These pipes are particularly valued for their corrosion resistance, which makes them ideal for use in harsh environments such as offshore drilling, petroleum extraction, and chemical processing.
Key Materials for Stainless Steel Seamless Casing Pipes
Stainless steel casing pipes come in various grades, each suited to specific applications. Below are the key materials used in their production:
TP304H
- Composition: Contains 18-20% chromium and 8-10.5% nickel, along with other trace elements like carbon.
- Properties: High resistance to oxidation and corrosion in a wide range of environments, including high-temperature settings.
- Applications: Used in heat exchangers, boilers, and other applications requiring high-temperature resistance.
TP310H
- Composition: Similar to TP304H but with higher levels of chromium (24-26%) and nickel (19-22%).
- Properties: Exceptional heat resistance and corrosion resistance, especially in high-temperature environments.
- Applications: Furnace parts, heat exchangers, and other equipment exposed to high temperatures.
TP316H
- Composition: Contains molybdenum (2-3%) along with chromium and nickel.
- Properties: Improved resistance to corrosion, especially in chloride environments, and excellent high-temperature properties.
- Applications: Chemical processing, food processing, and marine environments.
TP321H
- Composition: Includes titanium as a stabilizer, preventing carbide precipitation.
- Properties: Excellent resistance to intergranular corrosion at high temperatures.
- Applications: Aerospace, chemical processing, and high-temperature applications.
TP347H
- Composition: Similar to TP321H but with the addition of niobium (columbium).
- Properties: High strength and oxidation resistance at elevated temperatures.
- Applications: Ideal for applications in the power generation and chemical industries.
Understanding Pipe Sizes
The size of a stainless steel seamless casing pipe is defined by its Outer Diameter (OD), Thickness, and Length.
Outer Diameter (OD)
- The outer diameter of these casing pipes typically ranges from 4 1/2” to 20”, depending on the requirements of the application.
Thickness
- The pipe thickness can vary from 5.12mm to 16.13mm, which determines the pipe’s strength and ability to withstand internal and external pressures.
Length
- The pipes are available in various lengths:
- R1: 4.86m – 7.62m
- R2: 7.62m – 10.36m
- R3: 10.36m – 14.63m
Manufacturing Standards
Stainless steel seamless casing pipes are produced according to various international standards. Some of the key standards include:
- ASTM A213: Covers seamless ferritic and austenitic alloy-steel boiler, superheater, and heat-exchanger tubes.
- ASTM A376: Standard specification for welded austenitic stainless steel pipes.
- ASTM A511: Specifies seamless stainless steel mechanical tubing.
- ASTM A312: Standard specification for seamless and welded austenitic stainless steel pipes.
- DIN 17459: German standard for stainless steel pipes.
- EN 10216-5: European standard for seamless stainless steel pipes for pressure purposes.
- GOST 9941-81: Russian standard for seamless steel pipes for structural purposes.
Certificates and Approvals
Manufacturers of stainless steel seamless casing pipes often obtain certifications to ensure quality and compliance with international standards. Common certifications include:
- LR (Lloyd’s Register)
- BV (Bureau Veritas)
- DNV (Det Norske Veritas)
- GL (Germanischer Lloyd)
- ABS (American Bureau of Shipping)
- KR (Korean Register of Shipping)
- CCS (China Classification Society)
- TS (Turkish Standards)
- PED (Pressure Equipment Directive)
- AD2000: German standard for pressure equipment.
- ASME II & III: American Society of Mechanical Engineers standards for materials and fabrication.
Applications of Stainless Steel Seamless Casing Pipes
Stainless steel seamless casing pipes are used in a wide array of industries, including:
- Oil & Gas: For drilling and exploration purposes, as well as oil extraction systems.
- Power Generation: In steam and gas turbines, and in energy production facilities.
- Water Treatment: For filtration and transporting water.
- Chemical Industries: To carry chemicals, gases, and fluids without contamination.
- Marine & Offshore: For use in shipbuilding and offshore drilling platforms.
Benefits of Stainless Steel Seamless Casing Pipes
Corrosion Resistance
One of the primary benefits of stainless steel casing pipes is their exceptional resistance to corrosion. This is particularly important for applications in harsh environments such as offshore drilling platforms or chemical processing plants.
High Strength
Stainless steel is known for its ability to withstand high pressures and mechanical stresses, making it an ideal choice for pipelines that carry fluids or gases under high pressure.
Durability
These pipes offer excellent longevity, reducing the need for frequent replacements or repairs, especially in industries with high demands.
Types of Stainless Steel Seamless Pipes
In addition to TP304H, TP310H, TP316H, TP321H, and TP347H, there are other variations of stainless steel pipes, each offering different properties based on the alloy composition.
Surface Finishing of Casing Pipes
The surface finish of stainless steel casing pipes is crucial for improving their resistance to corrosion and enhancing their aesthetic appeal. Common surface finishes include:
- Mill Finish: The most basic surface finish, often used for industrial purposes.
- Pickled Finish: A treatment process that removes scale, improving corrosion resistance.
- Polished Finish: Provides a shiny, smooth surface, often used in decorative or sanitary applications.
Welding and Fabrication of Stainless Steel Casing Pipes
Welding stainless steel pipes requires special care to avoid compromising the material’s properties. Different welding techniques such as TIG (Tungsten Inert Gas) and MIG (Metal Inert Gas) are commonly used.
Quality Control in Manufacturing
Ensuring the highest quality in stainless steel casing pipes is paramount. Common tests and inspections include:
- Hydrostatic Testing: To check for leaks and determine the pipe’s ability to withstand high pressure.
- X-ray Inspection: For detecting internal defects.
- Dimensional Inspection: Ensures that pipes meet the specified thickness and diameter.
Packaging and Delivery
Stainless steel casing pipes are typically packaged in export-standard packaging, such as bundled wooden boxes, to prevent damage during transport. The packaging ensures the pipes are safe for transport by sea, air, or land.